- Visual check of the load
- Quantity check
- Cartons and pallets label marking check: product name, batch number, expiry date
- Visual control of potential damages
- Immediate identification and notification on receipt and special management of any discrepancies against delivery notes/packing lists
- Download temperature recordings and read out data
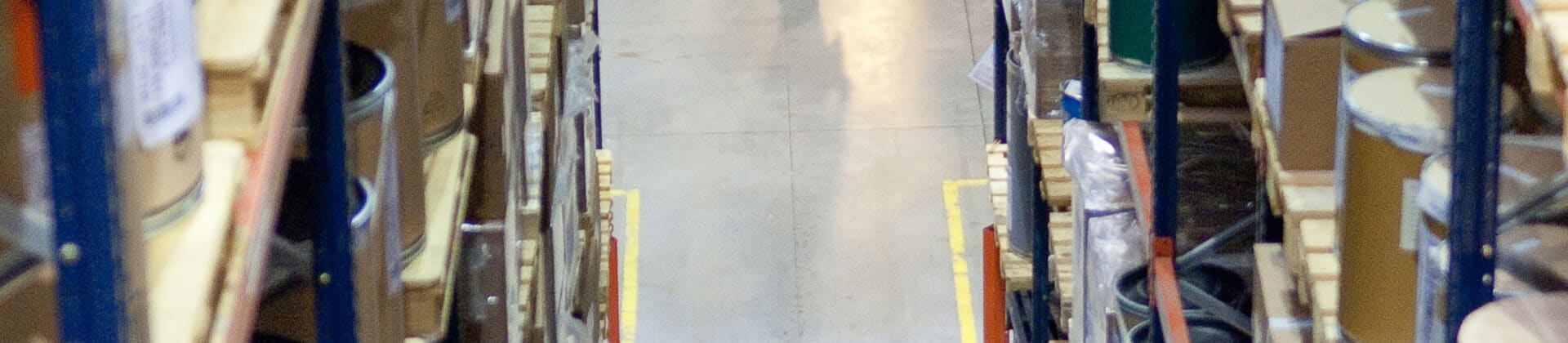
LOGISTICS
With more than 75 years of experience in the development and production of pharmaceuticals for some of the largest pharmaceutical companies in the world, Famar is the market leader in Greece in regard to distribution and logistics services. Famar currently provides services for various products (pharmaceuticals, consumer, medical devices, etc.) and multiple logistics profiles (bulk picking, box picking, item picking, micro-logistics, etc.).
Famar has unique know-how in the distribution of exclusively pharmaceutical and cosmetic products.
On annual basis, Famar processes approximately 900.000 orders, 6.000.000 order-lines, 250.000.000 packs, which are distributed to 12.500 different delivery points (451 Hospitals & Private Clinics, 140 Wholesalers, 11.000 Pharmacies, 900 other delivery points, such as doctors, microbiologists etc.) within the Greek territory. Regarding the Pharmacies channel, around 600 are served per day.
- Electronically attributed storage location for each storage unit (e.g pallet) according to temperature and other special storage requirements
- RF scanners use for putting away
- Product status handling (Quarantine / Release / Hold) by SKU and batch number
- Labeling of the Greek Authorities authenticity labels
- Repackaging / Secondary Packaging Activities for pharmaceutical products
- Batch record review
- Full reconciliation of packaging materials
- Authenticity Labels Handling
- Dedicated call centre managing passive and active order taking
- Customized designs based on specific requirements
- Received orders may be automatically executed or sent to our customers for review
- Stock controls and batch assignment
- Expiration Date handling (FIFO, LIFO, FEFO)
- Bulk, box and item picking
- Issuing and handling of order documentation (e.g. invoices, receipt advice etc.)
- Largest and most widely-spread pharmaceutical quality transportation network
- Fully GDP compliance supporting ambient (15o-25o C°), air contained (2o – 25o C°) and cold-chain (2o-8o C°) products
- Extensive network of cross-docking facilities, covering Northern, Central and Southern Greece
- Over 96% of the volume shipped is distributed via our GDP fleet
- Online Proof-of-Delivery on demand
- Debt – cash collection on delivery: Collection of payments on delivery shipments according to the customer’s commercial policy
- Validated cold rooms
- Validated refrigerated trucks
- Constant temperature monitoring
- Advanced services for specific products providing enhanced monitoring and handling from goods receipt to delivery
- Collection of the expired, damaged or obsolete products following the terms and conditions defined by our customers
- Recall management
- Complete tracking records for all product transactions
- Analytical product status handling (e.g. expired, damaged, nearly expired etc) by SKU and batch number
Customer Service Levels (KPI’s)
Complete set of KPI’s monitors the level of services. The areas covered and monitored are:
- Receiving time
- Stock accuracy
- On time Execution of orders
- Delivery effectiveness (cancelled orders by reason code)
- Accuracy of orders (picking errors)
- On time delivery
- Returned goods report (damaged, expired etc.)
System of Crisis Management / Business Continuity
- Comprehensive Business Continuity plan in place to enable the Distribution Centre to efficiently manage and quickly recover from emergency/crisis incidents and to ensure continuity of its core activities and critical services