At Famar, the main objective is to go beyond compliance and strive for:
- Innovating on Integrated Quality Management System via Digital Transformation – WE GO Digital
- Continuous development of a benchmark Quality Management System integrated in all sites to reliably deliver Quality Operational Excellence
- Agile Regulatory Intelligence and knowledge management towards proactive development of new services to best accommodate its customers
Integrated Quality
Management System
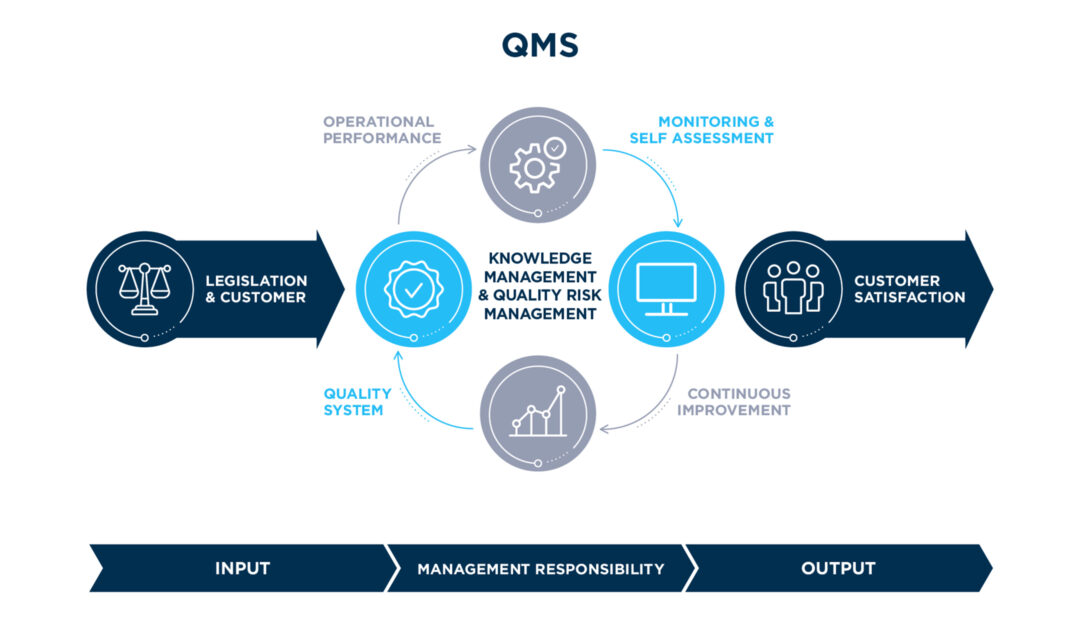
Legislation & Customer
Utilization of leading industry digital platforms on Regulatory Intelligence and Pharmaceutical Legislation Compliance towards a prompt readiness and interpretation of upcoming legislative requirements
Operational Performance
The overall effectiveness of manufacturing, distribution and development operations is continuously monitored and assessed by an integrated set of Quality Key Performance Indicators analyzed on a monthly basis to identify trends, explore opportunities for further improvement and benchmark operational excellence across Famar’s network of sites
Monitoring & Self Assessment
Applying a rigorous program of compliance self-assessment and integrated Inspections readiness across all Sites and supporting functions
Quality System Documentation
The foundation of Famar’s Integrated Quality Management System is the well-established set of Group Internal Policies & Guidelines delivered into site operations, in full compliance to Good Manufacturing & Distribution Practices, as well as Regulations of our exporting markets.
Continuous Improvement
Continuous Improvement and Famar Excellence Roadmap focusing on compliance, risk management, quality operations efficiency and cost reduction (e.g. Lean Lab Operations, Advanced Problem Solving)
Customer Satisfaction
Customer satisfaction via established KPIs, related to overall Famar Operational Performance and Quality Services provided
Famar’s Integrated Quality Management System is reviewed on a periodic basis in order to measure the achievement of its Quality Objectives & Key Results (OKRs), assess its Quality Metrics, monitor the effectiveness of its services & identify opportunities for continuous improvement of products, processes and the system itself.
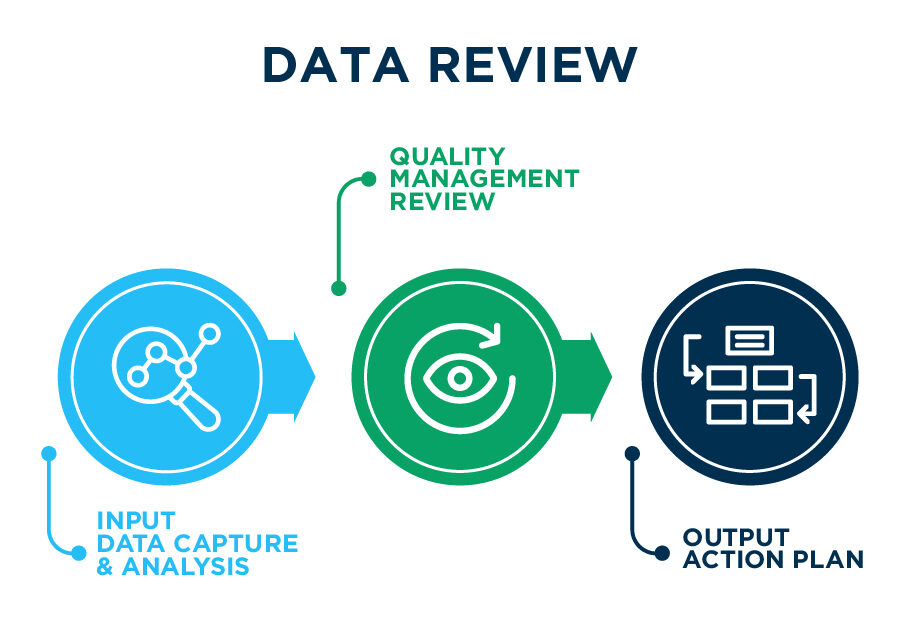
Input Data Capture & Analysis
Manage, monitor, trend and analyze data from the integrated Quality Management System Digital solutions in all operational units. Real time KPIs monitoring.
Quality Management Review
Application of adapted and Integrated Management by Objectives (MBO) and Objectives & Key Results (OKR) methodologies towards Operational Quality Performance Monitoring and Continuous Improvement
Output Action Plan
Highlight opportunities for growth, improvement, focused areas and self-assessments